1. Introduction
Choosing the right flange type is essential to ensuring the safety, reliability, and longevity of your piping system. Among the most commonly used options are the Slip On (SO) flange and the Weld Neck (WN) flange. Though both are designed to connect pipes, valves, and other components, they differ significantly in structure, strength, and suitability for various pressure and temperature conditions.
Slip On flanges are easier to install and cost-effective, making them suitable for low-pressure, non-critical systems. In contrast, Weld Neck flanges feature a long tapered hub and a butt-weld connection, offering superior strength, fatigue resistance, and performance in high-stress environments.
In this blog, we take a closer look at the key differences between Slip On and Weld Neck flanges, comparing them across eight critical engineering dimensions—from design and welding method to fatigue life, flow efficiency, and long-term cost. Whether you’re planning a new build or assessing flange slip on welding in an upgrade, this guide will help you make a confident, technically sound decision.
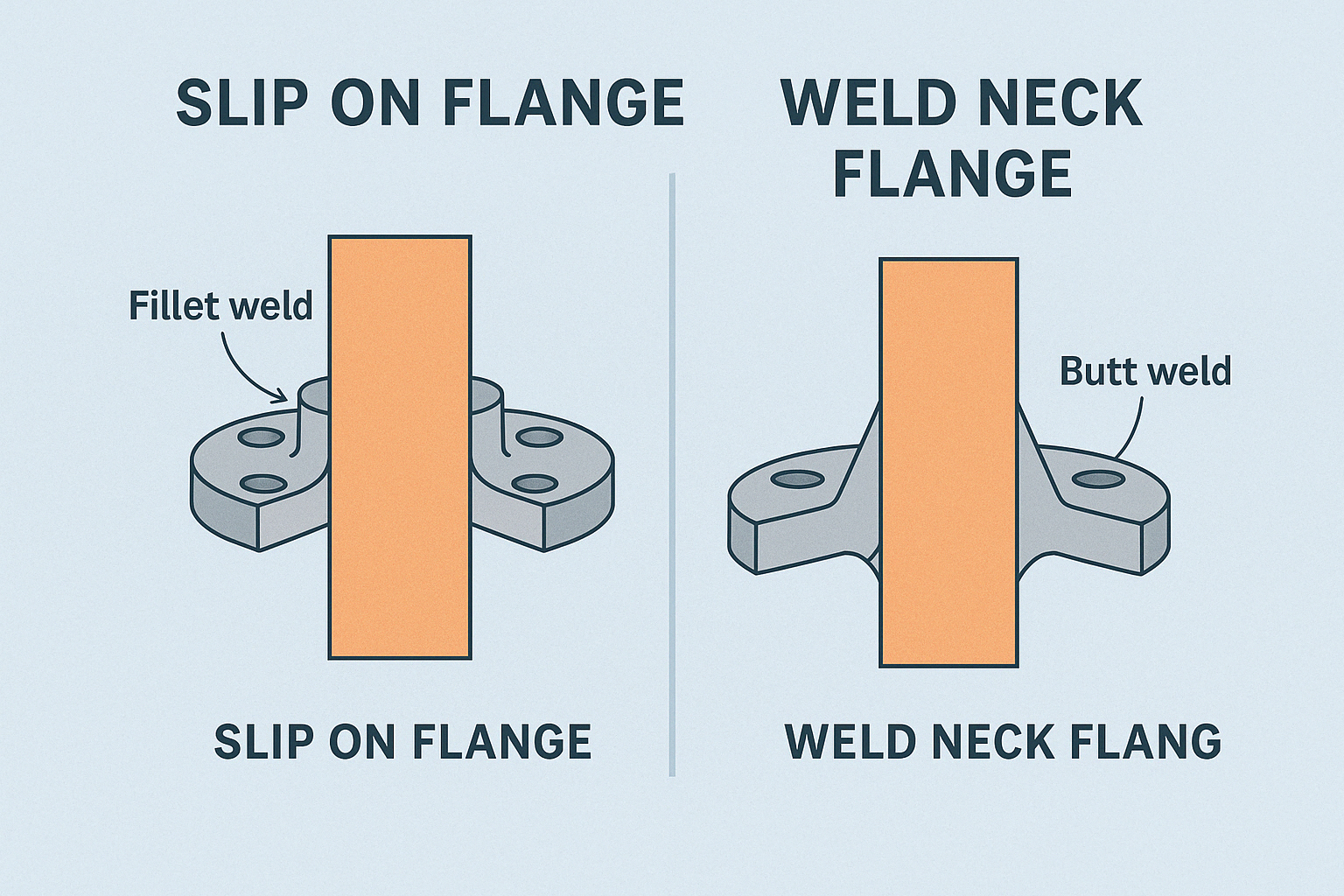
2. Design Differences: Slip On vs Weld Neck Flange
2.1 Slip On Flange
The Slip On flange is designed to slip over the pipe and is typically welded on both the inner and outer sides using fillet welds. It has a flat or slightly raised face and a short hub. The pipe is inserted into the flange bore, typically penetrating a short distance past the sealing face. This type of flange is often fabricated from steel plate flange materials and is commonly used in flat flange profiles.
Key Features:
- Simpler, shorter neck design
- No bevel preparation required
- Easy to align during installation
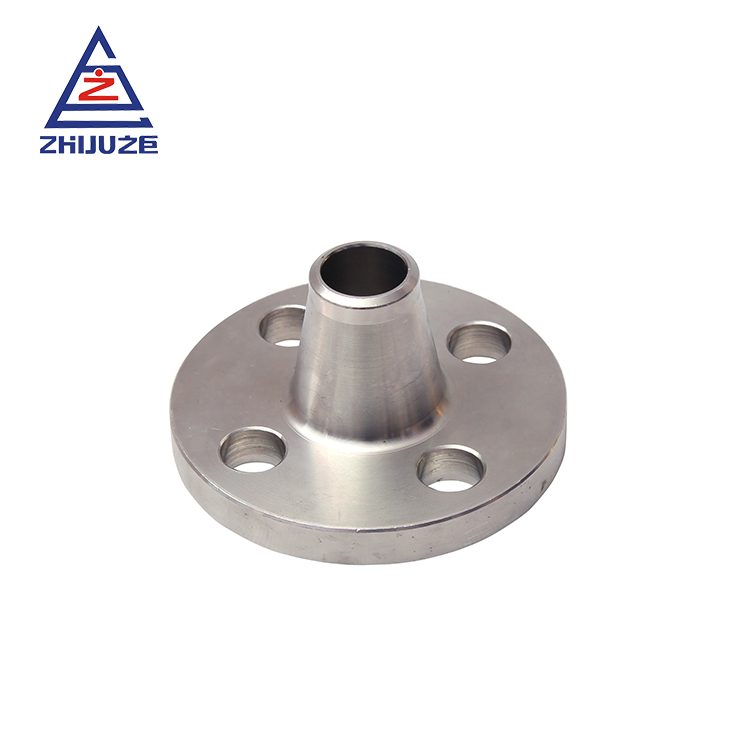
The Weld Neck flange features a long, tapered hub that gradually transitions into the pipe. It is connected using a butt weld, which aligns the flange bore and pipe bore, resulting in a smooth stress transition. It is typically manufactured as a forged steel flange, offering excellent structural integrity.
Key Features:
- Long tapered neck reduces stress concentration
- Requires precise bevel and alignment
- Ideal for critical applications involving high pressure pipelines
3. Welding Method & Structural Integration: Slip On vs Weld Neck Flange
3.1 Welding Method
- Slip On: Utilizes double fillet welds—one on the inside and one on the outside. While easier and faster to weld, it introduces more potential for crevice corrosion and less metallurgical bonding.
- Weld Neck: Uses a full-penetration butt weld. This welding technique requires skilled labor but results in stronger and more reliable joints, especially under fatigue loading. In both cases, proper flange slip on welding is crucial to prevent leakage.
3.2 Structural Integration
Weld Neck flanges are designed to integrate structurally with the pipe, distributing mechanical stress along the tapered hub. Slip On flanges, by contrast, have abrupt transitions that can cause localized stress points. This influences not only stress distribution but also fatigue resistance over time.
4. Strength and Fatigue Resistance: Slip On vs Weld Neck Flange
Strength and fatigue resistance are critical in systems exposed to cyclic loading, such as high-pressure steam pipelines or vibration-prone services.
Weld Neck Flange:
- Lower Stress Concentration Factor (SCF ~1.2-1.5)
- Butt weld ensures full load path continuity
- Demonstrated fatigue life of over 10^6 cycles under ±1.5 MPa pressure (approx. 220 PSI)
Slip On Flange:
- Higher SCF (~2.5-3.8)
- Prone to fatigue failure below 10^5 cycles in testing
- Higher risk of crack initiation at fillet welds
5. Flow & Pressure Loss: Slip On vs Weld Neck Flange
Flow performance is particularly important in high-speed and high-viscosity fluid systems.
Slip On Flange:
- Internal step or misalignment may cause turbulence and boundary layer separation
- CFD data shows loss coefficient (ζ) of 0.20–0.35
Weld Neck Flange:
- Smooth bore transition minimizes pressure drop
- ζ value typically in the range of 0.05–0.10, close to a straight pipe
- Reduces erosion risk and noise, supports higher pressure rating and temperature resistance
6. Installation Considerations: Slip On vs Weld Neck Flange
Slip On Flange:
- Easier to install, especially in tight or misaligned setups
- Requires less precise cutting and fitting
- Common in retrofit or temporary installations
- Ideal where flange replacement and repair may be frequent
Weld Neck Flange:
- Requires skilled welding and precise alignment
- Longer prep and weld time
- Preferred in permanent and mission-critical systems with high thermal expansion potential
7. Cost Comparison: Slip On vs Weld Neck Flange
Initial Cost:
- Slip On is more affordable in terms of materials and labour
- Less welding effort, fewer skill requirements
Long-Term Cost:
- Weld Neck offers better lifecycle value in critical systems
- Less downtime, lower maintenance, fewer failures
Conclusion: For budget-limited, non-critical systems, SO flanges are preferred. For durability, longevity, and performance, WN flanges win. This cost comparison demonstrates the importance of aligning flange selection with system priorities.
8. Typical Applications: Slip On vs Weld Neck Flange
Slip On Flanges:
- Firewater systems
- Cooling water pipelines
- Low-pressure utility lines
- Temporary pipework in construction
Weld Neck Flanges:
- High-pressure steam pipelines
- Process piping in oil refineries
- Chemical reactors and cryogenic services
- Power generation and nuclear systems
- Applications governed by ANSI standards and high pressure class requirements
9. Slip On vs Weld Neck: How to Choose Based on Use Case
When deciding between these two flange types, consider the following:
- Pressure & Temperature: Choose WN for high pressure rating and temperature resistance
- Fatigue Exposure: Use WN in cyclic loading conditions
- Installation Constraints: Choose SO for faster, simpler installs
- Cost Sensitivity: Use SO for budget-conscious projects
- Code Requirements: Certain codes (e.g., ANSI standards, ASME B31.3) may prefer WN
10. Conclusion
Both Slip On and Weld Neck flanges have their place in piping system design. While Slip On flanges offer simplicity and cost savings, Weld Neck flanges deliver superior performance, especially in critical applications where fatigue resistance, pressure, and long-term reliability are concerns. By evaluating your project needs through these eight engineering dimensions, you can confidently select the right flange for your system.